The Important Function of Tank Welding Assessment in Ensuring Structural Integrity and Security Conformity in Industrial Applications
In the world of commercial applications, tank welding assessment arises as a pivotal aspect in guarding architectural stability and making certain compliance with security policies. Making use of a combination of methods such as aesthetic assessments and advanced screening approaches, these evaluations offer to recognize and reduce potential imperfections before they escalate into significant hazards.
Significance of Storage Tank Welding Examination
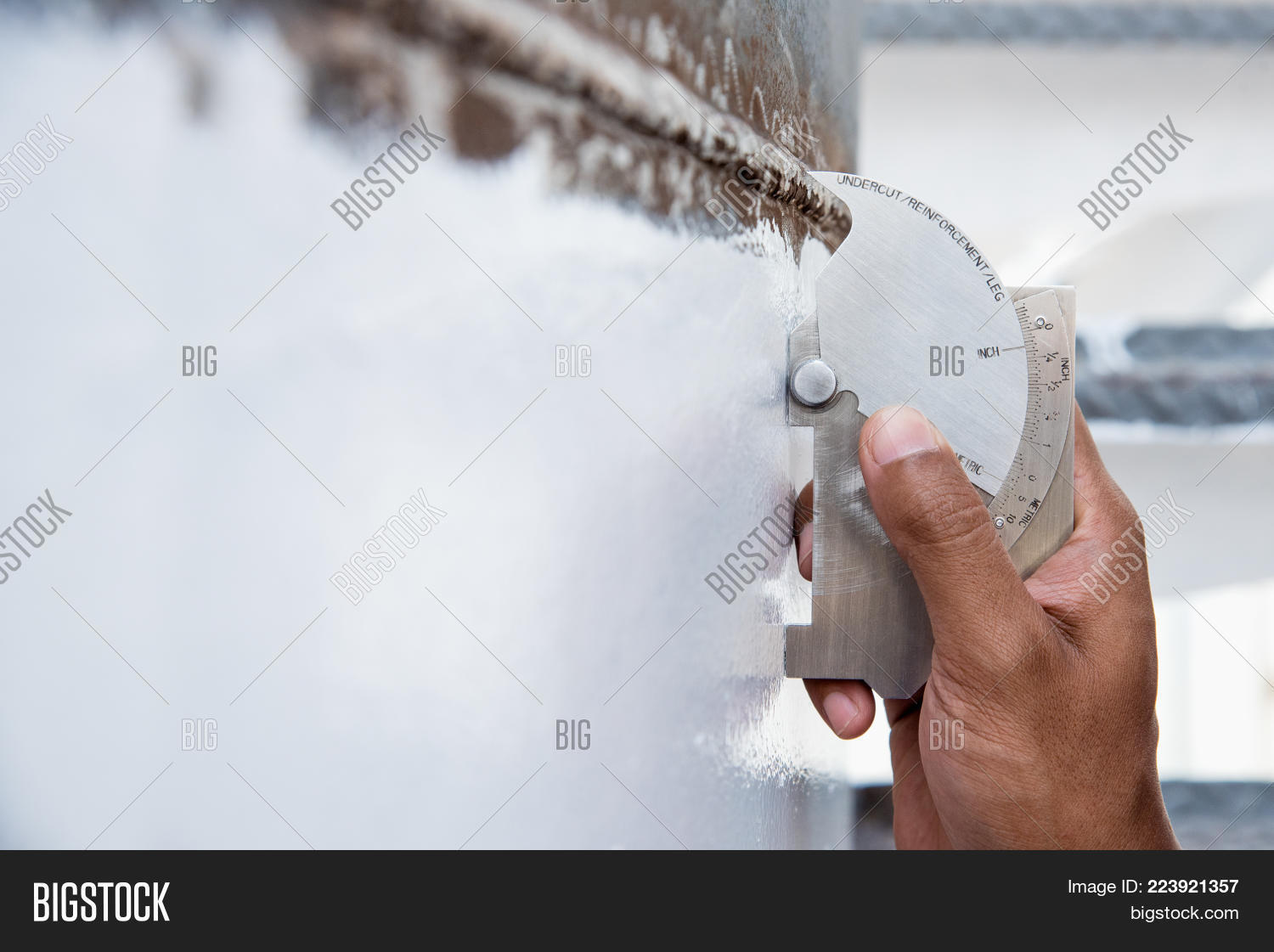
Making sure compliance with sector requirements and policies is one more considerable aspect of container welding inspection. Regulative bodies mandate rigorous standards for the building and construction and maintenance of tank, and comprehensive evaluations assist organizations follow these demands. Non-compliance can cause extreme charges, consisting of penalties and shutdowns, better stressing the demand for extensive examination methods.
Moreover, container welding examination plays a critical duty in keeping operational efficiency. Normal analyses can recognize prospective problems prior to they escalate, helping with timely repair services and decreasing downtime. This proactive approach not only boosts security but additionally adds to cost financial savings over time. In summary, the significance of container welding inspection depends on its capacity to safeguard public wellness, shield the atmosphere, and ensure compliance with governing frameworks.
Trick Inspection Methods
Efficient container welding inspection depends on a range of essential techniques that make certain detailed analysis of weld top quality and structural integrity. Among the most common strategies are visual inspection, ultrasonic testing, radiographic testing, and magnetic particle screening - Tank Welding Inspection. Each technique offers distinct advantages in analyzing various facets of the weld
Aesthetic inspection functions as the initial line of defense, allowing examiners to identify surface area issues, irregularities, or disparities in the weld grain. Ultrasonic testing uses high-frequency acoustic waves to detect inner problems, such as splits or gaps, offering a comprehensive assessment of weld integrity. This technique is particularly effective in spotting problems that might not show up externally.
Radiographic screening uses X-rays or gamma rays to generate photos of the welds, revealing inner gaps and offering an irreversible record for future recommendation. This technique is highly efficient for critical applications where the danger of failure must be reduced.
Lastly, magnetic bit testing is utilized to identify surface and near-surface issues in ferromagnetic materials. By using electromagnetic fields and great iron fragments, inspectors can pinpoint suspensions that could jeopardize the architectural stability of the container. Together, these strategies create a robust framework for making certain top notch welds in commercial applications.
Conformity With Safety Requirements

Regular examinations play an essential duty in guaranteeing conformity by identifying prospective failings or variances from prescribed standards. Examiners are trained to assess weld top quality, validate material requirements, and analyze the total structural honesty of storage tanks. Their expertise is important in ensuring that welding procedures fulfill the called for safety criteria.
Additionally, compliance with security criteria not only safeguards workers yet likewise safeguards the atmosphere from prospective hazards such as leakages or devastating failures. Organizations that focus on safety conformity are better positioned to alleviate risks, enhance functional effectiveness, and foster a society of safety within their workforce. In summary, preserving rigorous conformity with safety criteria is crucial for the effective procedure of tank welding activities in industrial setups.
Advantages of Regular Inspections
Routine inspections are integral to keeping the structural stability and safety and security of welded tanks. These inspections offer a methodical strategy to recognizing possible problems or weaknesses in the welds, guaranteeing that any type of concerns are addressed before they rise into significant failings. By conducting routine analyses, organizations can detect rust, exhaustion, and other kinds of wear and tear that might jeopardize storage tank efficiency.
Furthermore, constant examinations contribute to conformity with market regulations and standards. Complying with these standards not only mitigates lawful risks however likewise boosts the company's online reputation for security and reliability. Routine evaluations cultivate a positive safety and security society, encouraging staff members to recognize and prioritize the relevance of equipment honesty.
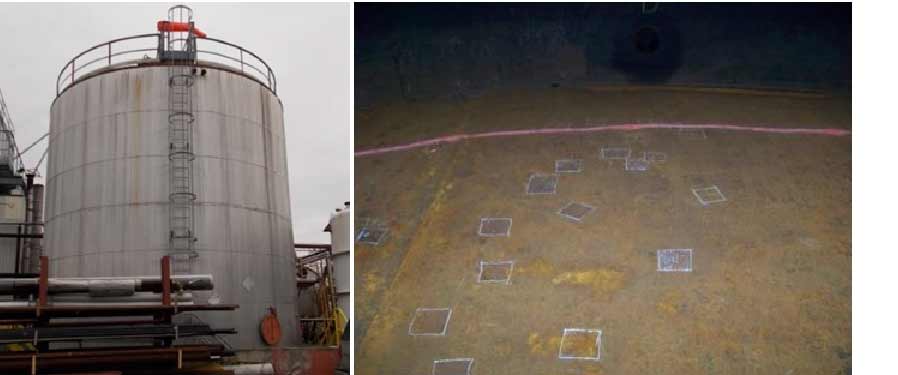
Study and Real-World Applications
Instance studies and real-world applications highlight the substantial effect of effective container welding assessment methods. Following the application of rigorous welding inspection methods, consisting of visual and ultrasonic find out here testing, the center identified critical imperfections in weld seams that could have led to disastrous failings.
Likewise, visit here a water treatment plant implemented a thorough assessment program for its tank welding operations - Tank Welding Inspection. By including non-destructive screening approaches, the plant was able to discover early signs of rust and tiredness in weld joints. This timely intervention prolonged the life-span of the tanks and ensured conformity with safety laws, thus guarding public health
These instance studies underscore the value of regular and systematic storage tank welding assessments. By focusing on these practices, industries can alleviate risks, improve architectural honesty, and guarantee conformity with safety standards, eventually leading to improved functional performance and reduced responsibilities.

Conclusion
In verdict, container welding examination is an indispensable part of keeping architectural stability and safety in commercial applications. Utilizing various examination strategies makes sure early discovery of possible problems, thus preventing disastrous failures.